Tvarovanie
Najpokročilejšie materiály z ocele s vysokou pevnosťou (AHSS) obsahujú špecifické chemické zloženie a mikroštruktúry s mnohými posilňovacími mechanizmami používanými na zvýšenie pevnosti, ťažnosti, húževnatosti a únavových vlastností. Aj keď sú tieto vlastnosti pre dizajnérov dobrou správou, pre výrobných inžinierov je výzvou tvarovanie týchto materiálov, či už ide o nosníky dverí za studena, komponenty sedadiel alebo nárazové skrinky; valcovacie nárazníky, vahadlá alebo pásy sedadiel; alebo za tepla tvoriace zložité časti odolné proti nárazu.
„Spring-back sa napríklad často považovalo za hlavnú prekážku pri razení AHSS, ale proces razenia za horúca toto riziko eliminuje,“ vysvetľuje Jean-Luc Thirion, generálny riaditeľ ArcelorMittal Global R&D. „Pri prvom vydaní boli materiály AHSS výrobcami OEM rýchlo rozpoznaní ako veľká príležitosť na zníženie hmotnosti vďaka ich veľmi vysokej pevnosti v ťahu v kombinácii s robustnosťou počas spracovania. Tento trend bol posilnený laserom zváraným polotovarom[LWB] technológia, ktorá môže kombinovať niekoľko stupňov razenia za tepla a optimalizovať tak správu nehôd. “
Valcovanie ultravysokopevnostných ocelí (UHSS) je ďalším spôsobom, ako riadiť spätné pruženie pomocou progresívneho ohýbania, a získateľné profily sú čoraz zložitejšie. Produktová rada MartINsite spoločnosti ArcelorMittal má v súčasnosti maximálnu UTS (konečná pevnosť v ťahu) 1 700 MPa, aj keď je pravdepodobné, že sa rozšíri. Jedným z faktorov úspechu týchto materiálov je ich nižšia celková cena, pretože proces tvárnenia valcovaním je podstatne lacnejší ako lisovanie dielov, ktoré majú konštantný úsek v dĺžke, napríklad bočné prahy alebo nosníky dverí.
Najnovšie materiály AHSS tretej generácie ponúkajú vylepšené kombinácie pevnosti a tvárnosti, avšak s nižším obsahom legovania, čo ešte viac znižuje náklady. Príkladom je nedávno predstavený Fortiform spoločnosti ArcelorMittal.
„Materiály AHSS tretej generácie dodávajú novú možnosť – lisovanie zložitých dielov za studena s triedami ocele nad 1000 MPa UTS za studena,“ uvádza Thirion. „Môžu nahradiť niektoré materiály AHSS staršej generácie, ako sú dvojfázové ocele, čo ponúka potenciálnu úsporu hmotnosti 10 – 20%.
„Špecifické mikroštruktúry spoločnosti Fortiform nám umožňujú kombinovať vynikajúcu globálnu tvarovateľnosť, meranú napríklad predĺžením, a vynikajúcu lokálnu tvarovateľnosť, ktorú je možné odhadnúť pomocou pomeru dilatácie diery,“ pokračuje. „Diferenciácia je v cykloch tepelného žíhania, ktoré sme vyvinuli na získanie najvhodnejšej kombinácie fáz. Dvojfázové ocele predchádzajúcej generácie boli kombináciou mäkkej fázy[ferrite] a tvrdá fáza[martensite] . Komplexný žíhací cyklus používaný na výrobu Fortiformu však dodáva zadržaný austenit, ktorý má kľúčovú úlohu pri zlepšovaní tvárnosti. “
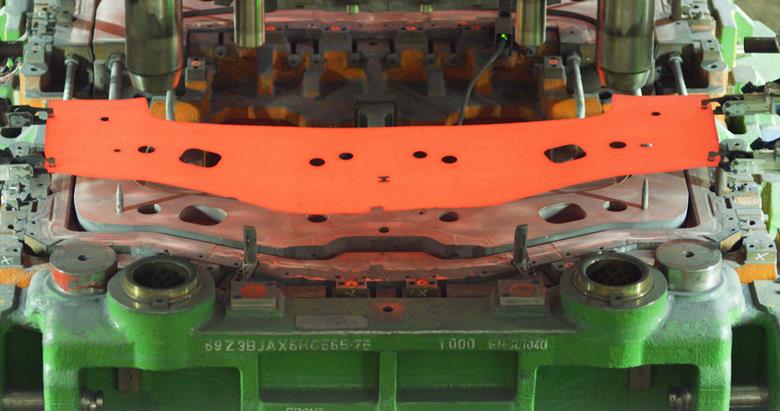
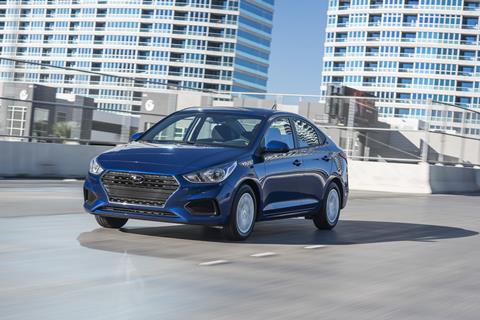
Dolaďovacie materiály
„Úzko spolupracujeme s automobilkami a najdôležitejšími dodávateľmi a starostlivo zvažujeme ich požiadavky v rámci našich programov vývoja produktov,“ hovorí Thirion. „Okrem toho často spolupracujeme na vývoji nových produktov vo veľmi ranom štádiu, aby sme pri dolaďovaní našich materiálov mohli zahrnúť ich prvú spätnú väzbu.“ Niekoľko výrobcov automobilov už implementovalo triedy Fortiform alebo HF (vysoká tvárnosť), napríklad Alfa Romeo pre Giulia a Peugeot pre 5008. Louis David, hlavný odborník na materiály a procesy pre vozidlá v PSA, hovorí o spoločnosti Fortiform: „Na našich vozidlách môžeme dosiahnuť zníženie hmotnosti za nulové alebo takmer žiadne dodatočné náklady. To je jeden z charakteristických znakov práce s oceľou. Väčšina ostatných riešení na zníženie hmotnosti je dosť drahá a stojí nás niekoľko eur za získaný kilogram. Vysoko pevnú oceľ alebo AHSS nahrádzame Fortiformom, pretože ponúka ešte vyššie mechanické vlastnosti pri rovnakej úrovni tvarovateľnosti. “
Rovnako nadšený je aj Fabio D’Aiuto, manažér oddelenia z FCA Metals ‚Group Materials Labs: „Fortiform je pre nás zaujímavý, pretože je to nový materiál, ktorý ponúka vysoký výkon, najmä pokiaľ ide o tvarovateľnosť. Potrebujeme zložité tvary a Fortiform 1050 nám to umožňuje dosiahnuť a za nižšiu cenu ako iné materiály.
„Tvárnenie za studena je spojené s dobrou tvárnosťou a dobrá tvárnosť je niečo, čo automobilky vždy hľadajú v oceli,“ pokračuje. „Odkedy sme začali používať Fortiform, nikdy sme nemali problém s výrobou alebo montážou.“ S pomocou spoločnosti ArcelorMittal a správnych matríc sa nám podarilo vytvoriť zložité diely, ktoré je možné bez akýchkoľvek zvláštnych požiadaviek použiť na bežnej výrobnej linke. “ Do budúcnosti ArcelorMittal očakáva postupné nahradenie konvenčných stupňov AHSS UHSS. Hovorí sa v ňom, že valcovanie martenzitických materiálov by malo rýchlo rásť, pretože výrobcovia OEM zvyšujú elektrifikáciu vozidiel.
„Vieme, že akumulátory budú v týchto vozidlách kritickými modulmi, pretože je mimoriadne dôležité chrániť akumulátory pred nárazmi,“ hovorí Thirion. „Pre túto aplikáciu sa čoraz viac požadujú ocele s ultravysokou medzou výťažnosti a martenzitické triedy valcovaného plechu poskytujú nákladovo efektívne riešenie na ochranu batérií.“
Podľa iného dodávateľa materiálu, spoločnosti SSAB, sú triedy AHSS tretej generácie klasickou definíciou sladkého miesta pre automobilky – vysoká pevnosť s lepšou tvárnosťou a lepšou použiteľnosťou. Tvárnosť znamená, že tieto ocele môžu byť tvarované za studena tak, aby poskytovali zložitejšie geometrie v porovnaní s AHSS prvej generácie, a môže im po tvarovaní ostávať v materiáli dostatočná ťažnosť na odolnosť voči nárazom. Materiály Docol AHSS od spoločnosti SSAB sú dostupné v mnohých variantoch, najnovším prírastkom je Docol HE, rad AHSS valcovaných za tepla so zlepšenou ťažnosťou hrán a výrazne zvýšenou miestnou tvárnosťou, kvalitou šmykových hrán a pomerom dilatácie.
„Vďaka jemnejšej mikroštruktúre a zlepšenej ťažnosti hrán umožňuje Docol HE tvarovanie súčastí s rezanými hranami bez rizika mikrotrhlín, otrepov alebo zlyhania, čo môže byť pri výrobe nákladné,“ vysvetľuje Daniel Sund, produktový manažér valcované v SSAB. Medzi cieľové komponenty patria diely podvozku, konzoly a sedadlá, ako aj komponenty v hnacích ústrojenstvách, spojkách, spojkách a všetkých ostatných častiach, ktoré sú označené vyrazeným okrajom.
Vylepšuje sa úroveň dodávateľov
Medzi tých, ktorí spracúvajú vysokopevnostné ocele, patrí Clamason Industries, britský špecialista na kovové výlisky, kde 50% podnikania tvorí automobilový priemysel. Spoločnosť formuje a pečiatkuje materiál typicky dodávaný spoločnosťami ako Tata a ArcelorMittal, od zvitku s hrúbkou 1,0 alebo 3,0 mm a do šírky 400 mm. Cievka sa napája na progresívne nástroje spoločnosti, kde sa vyrezáva a formuje a koniec je dokončený.
Spoločnosť Clamason, ktorá vo svojich pobočkách vo Veľkej Británii a na Slovensku zamestnáva 290 ľudí, vyrába diely pre zákazníkov prvého stupňa v automobilovom priemysle v množstve až 5 miliónov ročne. Pomôcť splniť požiadavky na priepustnosť je nedávna investícia do projektu spoločnosti Bruderer UK v hodnote 1 mil. £ (1,3 mil. USD) do nového 300-tonového stroja Zani Motion Master.
„300-tonový Motion Master nám dáva schopnosť dosiahnuť viac ako 80 zdvihov za minútu a prevziať oveľa väčšie a zložitejšie komponenty,“ vysvetľuje obchodný riaditeľ Ian Davies. „Rozhodli sme sa tiež pre riešenie na kľúč, ktoré obsahuje servopohon a odvíjaciu linku.“ Dôležité je, že lis má konštrukciu s rámom H, ktorá je vhodnejšia na spracovanie vysokopevnostných ocelí ako bežné koncepty rámu C. „Technológia Motion Master navyše mierne spomaľuje rýchlosť jazdy na spodnom konci zdvihu, aby sa zvýšila presnosť a zabránilo sa riziku rozbitia materiálu,“ hovorí Ian Davies. „To by mohlo znamenať, že vysokopevnostné oceľové komponenty spracovávame o niečo pomalšie ako bežné diely – rýchlosťou 45 za minútu namiesto 60 – aby sme sa uistili, že zodpovedajú požadovanej špecifikácii.“
Ian Davies naznačuje, že spracovanie vysokopevnostných ocelí si určite vyžaduje špeciálny súbor úvah: „Napríklad vo fáze skúšky uskutočniteľnosti musíme zvyčajne robiť úpravy nástrojov. Potrebné sú prísnejšie nástroje, pretože húževnatosť materiálu vedie k rýchlejšiemu opotrebeniu, ako by to bolo pri použití konvenčnej ocele. Normálne musíme navyše naniesť špeciálny náter na oblasti rezania nástrojov. “
Skúšky uskutočniteľnosti tiež pomáhajú určiť výšku kompenzácie, ktorá sa vyžaduje na vygenerovanie presných formulárov. Medzi vysoko pevné konštrukčné oceľové diely vyrobené v spoločnosti Clamason patria rôzne konzoly palubnej dosky a lakťových opierok, z ktorých mnohé ťažia z týchto materiálov, aby splnili výkonové štandardy nárazových skúšok.
Výrobcovia dodávateľského reťazca poskytujúci služby tvárnenia materiálov AHSS budú pravdepodobne v najbližších rokoch mimoriadne zaneprázdnení, pretože tieto zliatiny si osvojuje čoraz viac platforiem vozidiel. Honda Acura RDX z roku 2019 je príkladom, ktorý sa vďaka spolupráci spoločnosti s ArcelorMittal môže pochváliť prvým vnútorne-vonkajším krúžkom dverí UHSS na svete. Kombinácia piatich rôznych meradiel prístroja AriblorMittal Usibor 1500 UHSS vytvára vnútorný dverný krúžok RDX so štyrmi meradlami použitými vo vonkajšom krúžku.
Rôzne ocele Usibor sú dodávané do dodávateľského reťazca pred dodávkou do závodu ArcelorMittal Tailored Blanks v Detroite, kde prebieha podporná technológia nazývaná laserová ablácia. Po ablácii sú ocele zvarené k sebe a sú vybavené rôznymi procesmi kontroly kvality, ktoré zaisťujú presnosť. Polotovary sa potom posielajú na razenie za tepla do finálnej časti požadovanej automobilkou.
Kamkoľvek sa zvýšil obsah AHSS v Jeep Grand Cherokee v roku 2019, zatiaľ čo Ford uvádza to isté v prípade modelov ako Explorer a Fiesta, rovnako ako GM v prípade modelu Chevy Silverado z roku 2019. Volvo a ďalšie európske automobilky taktiež vo veľkej miere využívajú bórové ocele lisované za tepla. Spoločnosť Hyundai pre svoj model 2018 Accent navyše uvádza, že 54,5% karosérie tvorí AHSS – čo je o 13 percentuálnych bodov viac ako v prípade modelu predchádzajúcej generácie.
S týmto druhom dopytu sa skupina materiálov AHSS a UHSS rozrastie tak, ako sa budú vyvíjať v súlade s rôznymi výkonnostnými potrebami komponentov vozidla. Tieto zliatiny ocele, ktoré zvyšujú pevnosť a bezpečnosť, poskytujú tiež riešenia v oblasti palivovej efektívnosti, znižovania emisií, trvanlivosti a kvality, a to všetko pri dosahovaní nákladovo konkurencieschopnej ekonomiky.